Commercial Buildings
September 21, 2023—What WattIQ was doing when it joined the Wells Fargo Innovation Incubator (IN2) program is fairly different from what it does now. The lessons from IN2 helped them discover they needed to make a pivot that has since put it on a path to success.
While starting as a company focused on commercial building energy savings and reduction, WattIQ has reduced its focus, specializing now in lab equipment at research and development (R&D) facilities. That is because over time, the folks at WattIQ discovered it was incredibly difficult to build a business just saving their clients miscellaneous kilowatt hours. Only certain classes of businesses and equipment could save enough total energy to make it worth what WattIQ had to offer.
The pivot focused on the use of sensors to help lab equipment run longer and more efficiently.
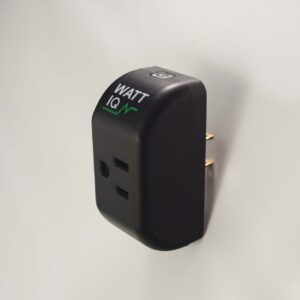
An easy-to-install advanced sensor that pairs with a Cloud system to predict equipment failures and optimize usage to save clients on energy and maintenance costs.
Photo courtesy of WattIQ
“With our sensors, we help people understand when things are going to fail before they fail,” WattIQ CTO Mark Madsen said. “We run a cloud-based service that uses sensors to understand how their equipment is used, and the health of their system. The idea is to reduce the cost of owning and maintaining large fleets of lab equipment.”
WattIQ’s clients include some of the largest pharmaceutical companies in the world, so it uses a combination of temperature, power, and other sensors to understand when the equipment is functioning properly and when it needs service.
WattIQ has two lines of business, learning how people use equipment and how well the equipment is performing. This means, first and foremost, maintenance prediction and prevention, but also reducing energy waste and improving efficiency.
One of the major problems WattIQ attempts to solve is human error. Machines are designed to make our lives easier, but they still require human interventions to shut down properly, activate maintenance mode, or ensure it is clean. If not properly cared for, these expensive resources can become repair-heavy investments that users are loathe to fix rather than replace.
Madsen specifically pointed to a cell analyzer, which lets scientists image and analyze individual cells. Each one costs $75,000, and each lab may have dozens of them. Each can also cost more than half a million dollars in maintenance, repairs, upkeep, and replacement parts during the first five years of its life. When these errors began to occur, many scientists simply asked for a new machine.
“There’s lots of waste,” Madsen said. “We are helping not only to elongate the lifecycle, but also achieve better usage over time. Customers can look at how the equipment is used to reduce the costs of maintenance.”
Many companies default to signing up for costly service contracts thinking that will minimize disruptions. WattIQ can examine the usage pattern for a piece of equipment and may discover the machine is only utilized a few times a month. Knowing that, the company can reduce their level of service and save thousands of dollars.
WattIQ also helps to monitor wasted energy, which is especially key for pharmaceuticals based in Europe where energy is often more expensive.
“Some of our pharmaceutical companies in Switzerland and Sweden want to identify where energy waste is,” Madsen said. “The equipment shouldn’t waste energy if used the way it’s intended, but how do they know if that’s happening? You have to monitor it.”
WattIQ joined IN2 back in 2016 and credits the program with laying the building blocks of where the company is today. Researchers at the National Renewable Energy Laboratory (NREL) helped WattIQ develop algorithms that look at plug loads and decide when it is acceptable to shut equipment off. WattIQ observed a building on the NREL campus for many years, ultimately making it easier for personnel who work there to determine when they should turn on and off equipment.
“That’s not about characterizing equipment, it’s about characterizing human behavior, which is variable and hard to predict,” Madsen said. “However, we have scheduling functionality in our system today and it really dates from the work we did with IN2 and NREL.”
The pivot for WattIQ came in 2019 when a large pharmaceutical company contacted the company, asking about power and cost savings. That pharmaceutical company became one of the first and larger COVID vaccine manufacturers, which means it uses many coolers that need to run constantly. The company asked WattIQ for power monitoring, and what seemed simple turned into a multi-year journey through COVID. After developing better algorithms for this type of equipment, WattIQ now monitors 3,000 coolers at one facility.
Madsen hopes this year will be the company’s best yet.
“This is a good year for us,” he said. “While what we do is not classical sustainability, we need to think about sustainability along more of an axis than we do today. You can improve sustainability in ways that don’t look like classic green energy plays.”
